Jun 7, 2024 | ABCO Systems, AGV, AMR, AS/RS, Automation, Robotics
ABCO Systems is thrilled to announce a groundbreaking strategic partnership with URBX, a pioneering robotic startup renowned for its innovative order fulfillment solutions. This collaboration is poised to bring transformative efficiency and accuracy enhancements to our customers, marking a new era in warehouse automation.

URBX has rapidly emerged as a game-changer in the industry with their cutting-edge fulfillment system, which features a double deep storage configuration and an ultra-efficient conveyor system. Their innovative approach maximizes space utilization while streamlining the picking of totes or containers, resulting in unprecedented levels of efficiency and accuracy.
By joining forces, ABCO Systems and URBX will combine their expertise to create a powerful synergy that will drive growth and success for both organizations. ABCO’s deep knowledge and experience in warehouse automation, coupled with URBX’s high-density and high-speed robotic Goods-To-Person System, will enable us to deliver state-of-the-art solutions that turn supply chains into competitive advantages for brands and retailers.
“Our partnership with URBX is a great milestone for both companies,” said Seth Weisberg, CEO at ABCO Systems. “Together, we will be delivering cutting-edge technology to today’s material handling automation, bringing innovative solutions that will elevate our offerings and deliver greater value to our customers’ operations.”
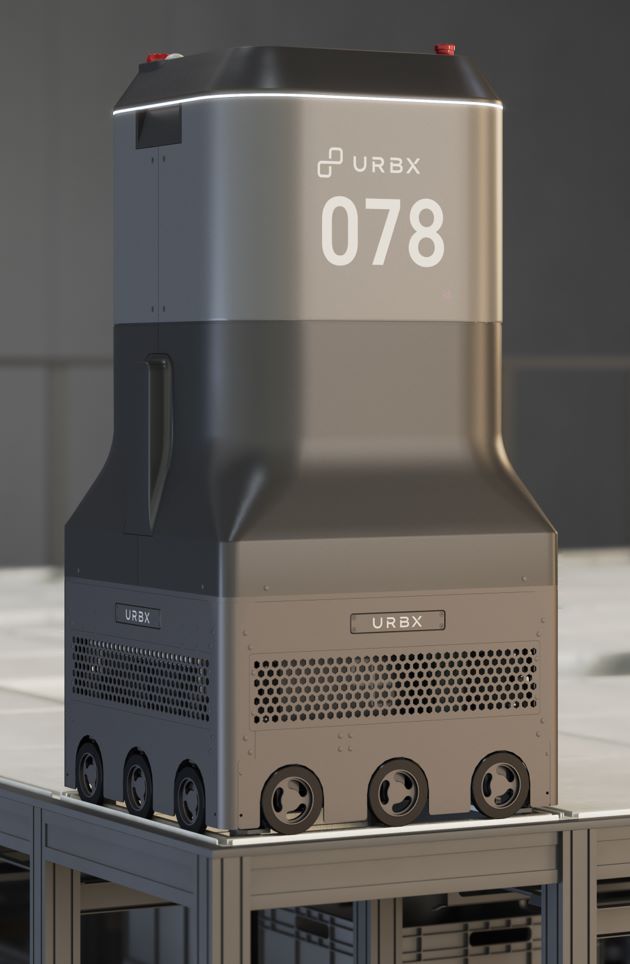
“This collaboration not only strengthens our capabilities but also aligns with our mission to continually push the boundaries of what is possible in warehouse automation. We are excited about the possibilities this partnership holds and look forward to sharing more updates on how we will elevate our service offerings through this strategic collaboration.”
Stay tuned for more news on how ABCO Systems and URBX will transform your warehousing operations and drive your business toward unparalleled efficiency and success.
About URBX:
URBX is an innovative robotic startup that provides high-density and high-speed robotic order fulfillment solutions. Their advanced systems are engineered to maximize space utilization and streamline the picking process, delivering exceptional efficiency and accuracy to warehouse operations.
Learn more about URBX on: urbx.com
Jan 2, 2024 | 3PL, ABCO Systems, AGV, AMR, AS/RS, Automation, E-commerce, Goods-to-person, order fulfillment, Robotics, space optimization
Picture this – it’s a crisp morning in January, and you stand at the entrance of your warehouse, eager to kick off another year of growth for your business. The dawn of a new year is the perfect opportunity to reflect on past achievements and set the stage for transformative changes. As the world of logistics and warehousing continues to evolve at a rapid pace, it is our firm belief that the resolution for 2024 should be to embrace smart strategies for a smarter warehouse. Let’s delve into the 4 key trends, backed by compelling statistics, that are reshaping the landscape for warehouse managers, logistics professionals, 3PL managers, Ecommerce Managers, Fulfillment Managers and many others engaged in supply chain.
Embracing Automation and Robotics
In a recent study conducted by Statista, the global warehouse automation market was valued at over 23 billion U.S. dollars in 2023. It is expected that the market will grow at a CAGR of about 15 percent in the following years and reach the size of 41 billion U.S. dollars in 2027, a testament to the accelerating demand for streamlined operations. As we bid farewell to static storage technologies, the emphasis on automation and robotics becomes paramount. By integrating Automated Guided Vehicles (AGVs) and Autonomous Mobile Robots (AMRs) into your warehouse fleet, you not only boost efficiency but also enhance the overall safety of your team. These technologies offer a dynamic solution for material handling, allowing for swift adaptability to changing demands.
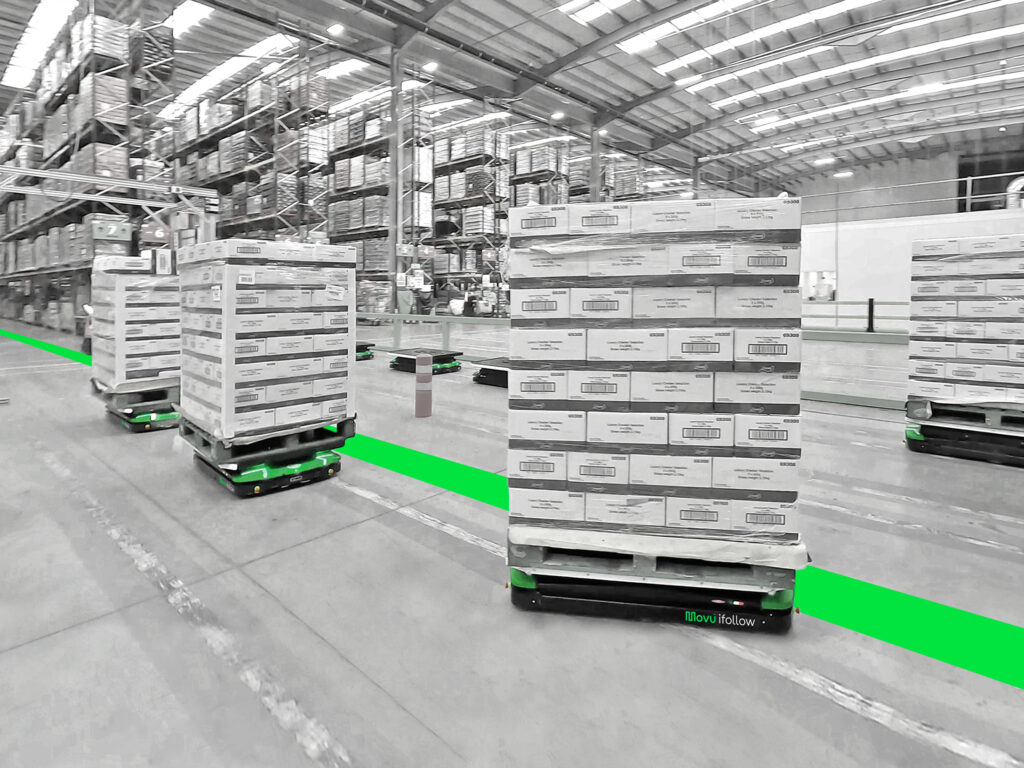
Picking Technologies that Redefine Speed and Accuracy
Accurate and speedy order fulfillment is the cornerstone of customer satisfaction, and in the evolving landscape of ecommerce, these two aspects of supply chain have become non-negotiable. According to a report by McKinsey, warehouses equipped with advanced state-of-the-art picking technologies experience a 20% increase in order accuracy. Imagine the impact on your bottom line when every package is delivered correctly the first time. Modern solutions, such as advanced Pick-to-Light technology and Pick/Put Walls, are reshaping the picking process, reducing errors, and ensuring your customers receive their orders promptly and accurately.
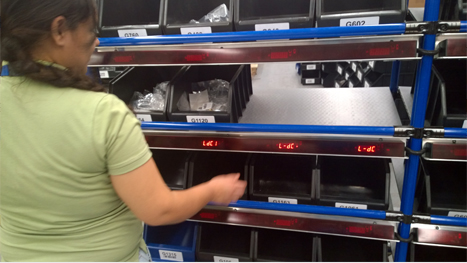
Responsive Warehousing in the Age of Ecommerce
In the era of one-click shopping and next-day delivery expectations, responsiveness is a key differentiator for warehouse managers. A study by Deloitte highlights that companies with highly responsive supply chains grow revenue 10% faster and reduce costs by 30% more than their peers. This New Year, consider the implementation of Automation and Robotics, combined with appropriate Warehouse Execution Systems (WES) that can seamlessly integrate with your existing infrastructure, optimizing task prioritization, resource allocation, and order fulfillment. Responsive warehouses not only meet customer expectations but also stay ahead of market trends.
Optimizing Footprint and Reducing Costs
An increase in order volume or expansion of operations and SKUs, often prompts the need for more warehouse space. However, since warehouse space has been at a premium for some time now, the resolution for 2024 is to optimize within your existing footprint. By reassessing and redesigning your current layout, as well as deploying new solutions like high-density automated storage systems, you can maximize vertical space and reduce the need for extensive horizontal expansion. This strategic approach not only curtails costs associated with additional square footage but also enhances overall operational efficiency.
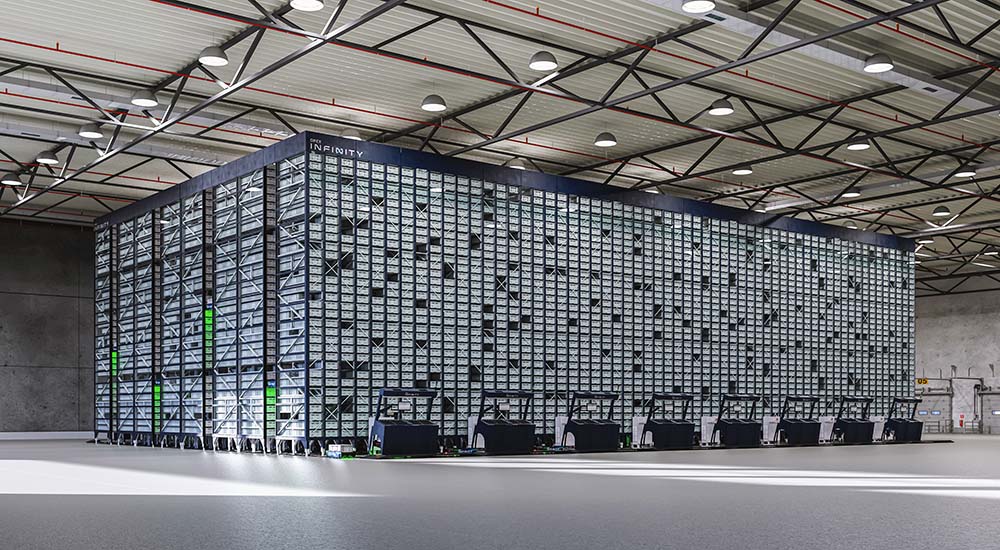
Conclusion
As you embark on this journey to build a smarter warehouse in 2024, remember that the right partner can make all the difference. ABCO Systems is a material handling integrator company with a proven record of incorporating cutting-edge automation, robotics, and picking technologies, thereby empowering your team to achieve higher accuracy, responsiveness, and growth – all within your existing footprint. Make this New Year resolution not just a commitment to change but a promise to revolutionize your warehouse for sustained success. Here’s to a year of smart strategies and smarter warehouses!
Dec 5, 2023 | ABCO Systems, AGV, AMR, Automation, Robotics, Systems Integrator
In the ever-evolving world of logistics and supply chain management, the adoption of warehouse robotics stands out as a transformative leap toward operational efficiency and agility. The prospect of increased productivity, accuracy, and streamlined processes has spurred businesses to explore the integration of robotics into their warehouse operations. However, the path to realizing these benefits is not without its challenges. In this blog post, we dive into the intricacies of implementing warehouse robotics, shedding light on the common hurdles that businesses encounter and presenting practical, actionable solutions to overcome them.
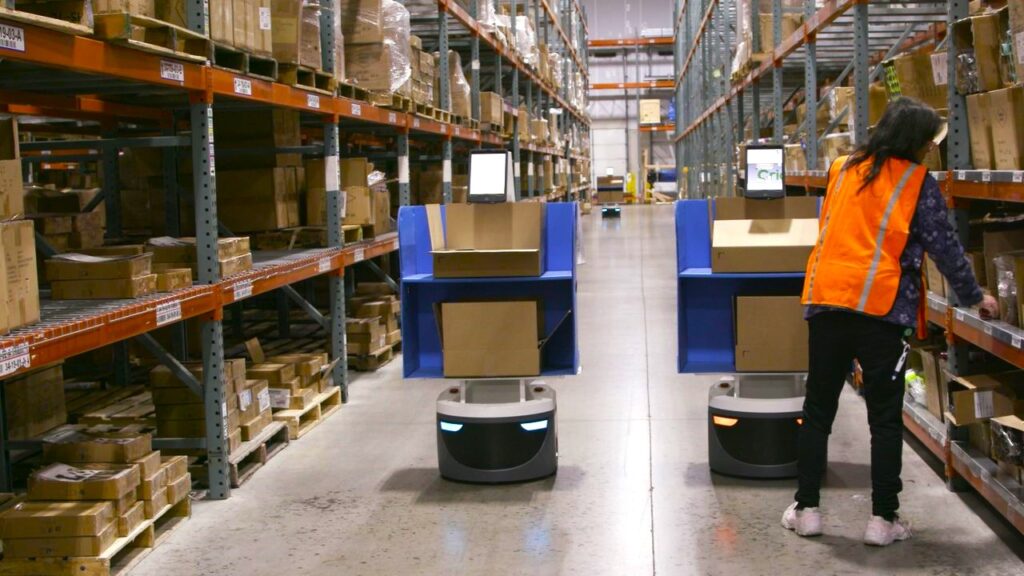
1. Integration Challenges
Challenge: Seamlessly incorporating warehouse robotics into existing operational ecosystems poses a significant challenge for businesses. The fear of disrupting well-established workflows and the complex nature of aligning robotic systems with diverse operational elements can present a formidable obstacle.
Solution: Begin by conducting a thorough system audit to pinpoint potential integration points. This involves a comprehensive analysis of existing processes, technologies, and infrastructure. Collaborating closely with experienced system integrators such as ABCO Systems, who bring their expertise in navigating the complexities of integration is highly advisable. Adopt a phased implementation approach, allowing for incremental integration rather than a sudden overhaul. This not only minimizes disruptions but also provides a learning curve for the workforce, ensuring a smoother transition.
Choose modular robotic systems that are designed to interface seamlessly with diverse warehouse technologies. These modular solutions allow for a step-by-step integration process, allowing businesses to leverage the advantages of robotics without an immediate, wholesale transformation. Additionally, try to establish clear communication channels between the robotic systems and existing warehouse management systems (WMS) to ensure real-time data exchange and synchronization.
Real-world Example: A distribution center facing integration challenges opted for an initial deployment of autonomous mobile robots (AMRs) to handle specific repetitive tasks, gradually expanding their robotic fleet as employees became acclimated to the new technology. This phased approach not only reduced integration complexities but also allowed the workforce to witness tangible benefits, fostering a positive attitude towards further adoption.
2. Employee Concerns
Challenge: The implementation of warehouse robotics may encounter resistance and concerns among the workforce. Employees can harbor fears of job displacement, uncertainties about their roles in a robotic-centric environment, or simply anxiety about adapting to a workplace where humans and robots coexist.
Solution: Addressing employee concerns is pivotal for the successful integration of warehouse robotics. Open, transparent communication is paramount. Initiate comprehensive training programs that not only educate employees about the new robotic systems but also emphasize their collaborative role alongside these technologies. Highlight the fact that robotics is not a replacement but a valuable addition that allows employees to focus on more strategic and fulfilling tasks.
Encourage a culture of inclusivity by involving employees in the implementation process. Seek their input and feedback, making them active participants in the transformation. Demonstrating how robotic systems can enhance job satisfaction by relieving them of monotonous, repetitive tasks allows employees to embrace the technology as a tool that augments their capabilities rather than a threat to their roles.
Real-world Example: A fulfillment center successfully managed employee concerns by organizing workshops and training sessions on the benefits and functionalities of warehouse robotics. This not only demystified the technology but also showcased how it could enhance job roles by eliminating mundane tasks. As a result, employees became advocates for the technology, actively contributing to its successful integration and dispelling initial apprehensions.
3. Cost Considerations
Challenge: The initial investment required for adopting warehouse robotics can be perceived as a significant financial hurdle. Businesses may be apprehensive about committing to the upfront costs associated with implementing robotic systems.
Solution: Overcoming cost considerations involves a strategic evaluation that extends beyond immediate financial outlays. Conduct a comprehensive cost-benefit analysis that weighs the upfront investment against the long-term gains in efficiency, accuracy, and labor optimization. Consider not just the immediate ROI but the sustained benefits that robotic systems offer over time.
Explore financing options that align with the financial goals of the business. Many robotics providers offer flexible financing plans or even leasing options that can alleviate the burden of a substantial upfront investment. Collaborate closely with experienced consultants to understand the tax incentives and potential cost-saving benefits associated with adopting robotic technologies, as well as to explore leasing arrangements.
Real-world Example: A distribution center successfully addressed cost concerns by working closely with ABCO Systems to find a robotics provider that offered a phased plan based on achieved milestones in operational efficiency. This not only made the initial investment more manageable but also ensured a mutually beneficial, long-term partnership where costs were aligned with the realized benefits of the robotic implementation.
4. Maintenance and Downtime
Challenge: Fears about maintenance requirements and potential downtime can be significant roadblocks when considering the adoption of warehouse robotics. Businesses are often concerned about the ongoing operational costs and disruptions that may arise due to maintenance needs.
Solution: Mitigating concerns related to maintenance and downtime requires a proactive and strategic approach. Choosing partners that offer comprehensive support and maintenance packages is essential. This ensures that any potential issues are swiftly addressed, minimizing the risk of prolonged downtime. A great strategy would be to mplement preventative maintenance schedules while utilizing data analytics. This allows you to anticipate maintenance needs based on real-time data, preventing unexpected breakdowns, and reducing the overall impact on operations. Training in-house teams to perform routine maintenance tasks also reduces dependency on external support and accelerates issue resolution.
Invest in robotic systems with modular designs that provide easy component replacements. This minimizes the time required for maintenance and allows for quick repairs without disrupting the entire system. Collaborate closely with the provider to develop a customized maintenance plan tailored to the specific needs and operational patterns of your business.
Real-world Example: A warehouse successfully addressed maintenance concerns by adopting a preventative maintenance approach. Utilizing sensor data from the robotic systems, the warehouse implemented a predictive maintenance schedule that anticipated issues before they led to downtime. This not only reduced maintenance-related disruptions but also extended the lifespan of the robotic equipment, optimizing the overall efficiency of the warehouse operations.
5. Scalability Concerns
Challenge: Businesses contemplating the adoption of warehouse robotics often grapple with concerns about the scalability of these systems. The fear that the chosen robotic solutions may not effectively scale with business growth can be a valid apprehension.
Solution: Addressing scalability concerns requires a forward-thinking approach that aligns robotic solutions with the evolving needs of the business. Opting for robotic systems that are inherently designed for scalability such as modular robotic solutions can be one such solution. These systems are capable of seamless expansion or upgrades, providing you the flexibility needed to accommodate increasing operational demands.
Collaborate closely with consultants to develop a roadmap for scaling robotic operations in tandem with business growth. This involves not just adding more robotic units but ensuring that the entire system, including software and infrastructure, can efficiently handle the heightened demands. Regularly reassess and adjust the robotic fleet based on evolving business requirements, leveraging the agility that modular designs offer.
Prioritize compatibility and interoperability when selecting robotic systems. The ability of new robotic additions to integrate smoothly with existing systems ensures a cohesive and scalable robotic ecosystem. Regularly evaluate the performance of the robotic systems in conjunction with business growth, making data-driven decisions to optimize the scalability of the entire warehouse operation.
Real-world Example: A distribution center effectively tackled scalability concerns by implementing a modular robotic system that allowed for the incremental addition of robotic units based on seasonal demands. This not only accommodated peak periods seamlessly but also provided the scalability needed to adapt to fluctuating business requirements. The modular approach ensured that scalability was not just a future consideration but an ongoing, dynamic aspect of their warehouse robotics strategy.
Conclusion
Warehouse robotics represent the future of efficient and streamlined operations, but success hinges on addressing and overcoming challenges proactively. By working with experienced integrators such as ABCO Systems and by embracing integration strategies, nurturing employee buy-in, conducting thorough cost assessments, implementing robust maintenance protocols, and ensuring scalability, businesses can navigate the transformative journey of adopting warehouse robotics with confidence. The key lies not just in adopting technology but in orchestrating a holistic shift towards a future where humans and robots collaborate seamlessly to achieve operational excellence. Reach out to us today to get started!
Nov 9, 2023 | AGV, AMR, Automation, Conveyor, Robotics
Businesses are looking for ways to maintain and improve efficiency while keeping costs low. In the realm of material handling and warehousing, one solution that has turned out to be a game changer is automation. Automation technology is still evolving rapidly but the latest systems are already very powerful, flexible, and easily scalable while becoming increasingly more affordable.
In this sense, entry-level automation offers a very attractive option for businesses looking to stay competitive in a challenging economic environment. Automation systems can seamlessly scale as your business grows, allowing you to manage peak periods and volume increases without major capital expenditures or infrastructure changes. They can also be reprogrammed to take on a wide variety of tasks in a warehouse environment. Their flexibility allows you to start small, experience the benefits, and then scale up as your business grows and finances become more available. It’s a smart investment that delivers tangible results.
Faster Picking, Less Walking, Higher Worker Satisfaction and Lower Cycle Time
With entry-level automation, you can considerably improve your picking processes. By automating mundane tasks and reducing manual labor, your workers can focus on higher-value activities, leading to faster picking times and lower operating costs. You can also say goodbye to wasted time and unnecessary walking in your warehouse. And when your employees are empowered to contribute more meaningfully to the business, the job satisfaction improves significantly. With automation solutions, you can optimize your storage and retrieval processes, reducing cycle times and maximizing picking efficiency. More time spent picking means increased throughput, high productivity and improved customer satisfaction.
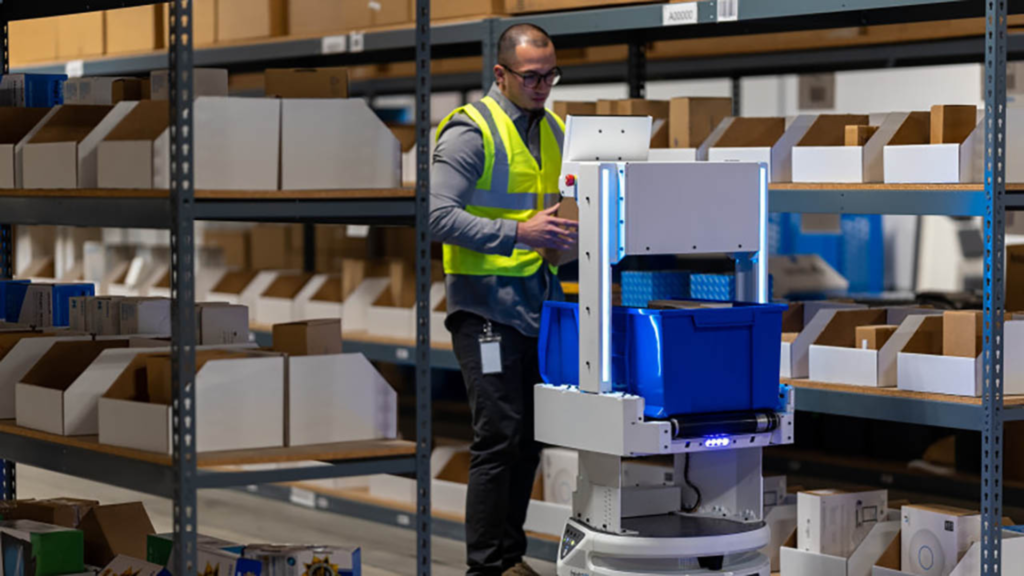
Rapid Deployment, Zero Disruption, Easy Integration
Implementing entry-level automation solutions has never been easier. New automation tech integrates seamlessly with your existing warehouse infrastructure, quickly configures to the way your organization already work and matches your workflow, routines, and processes. The latest Autonomous Mobile Robots – AMRs & Automated Guided Vehicles – AGVs for example can be deployed in days with onboarding of workers done in minutes. This allows you to experience the benefits quickly without significant disruption to your existing operations. Integration with existing WMS has also become a breeze, with additional flexibility to integrate special peripherals and accessories to expand functionality and usability.
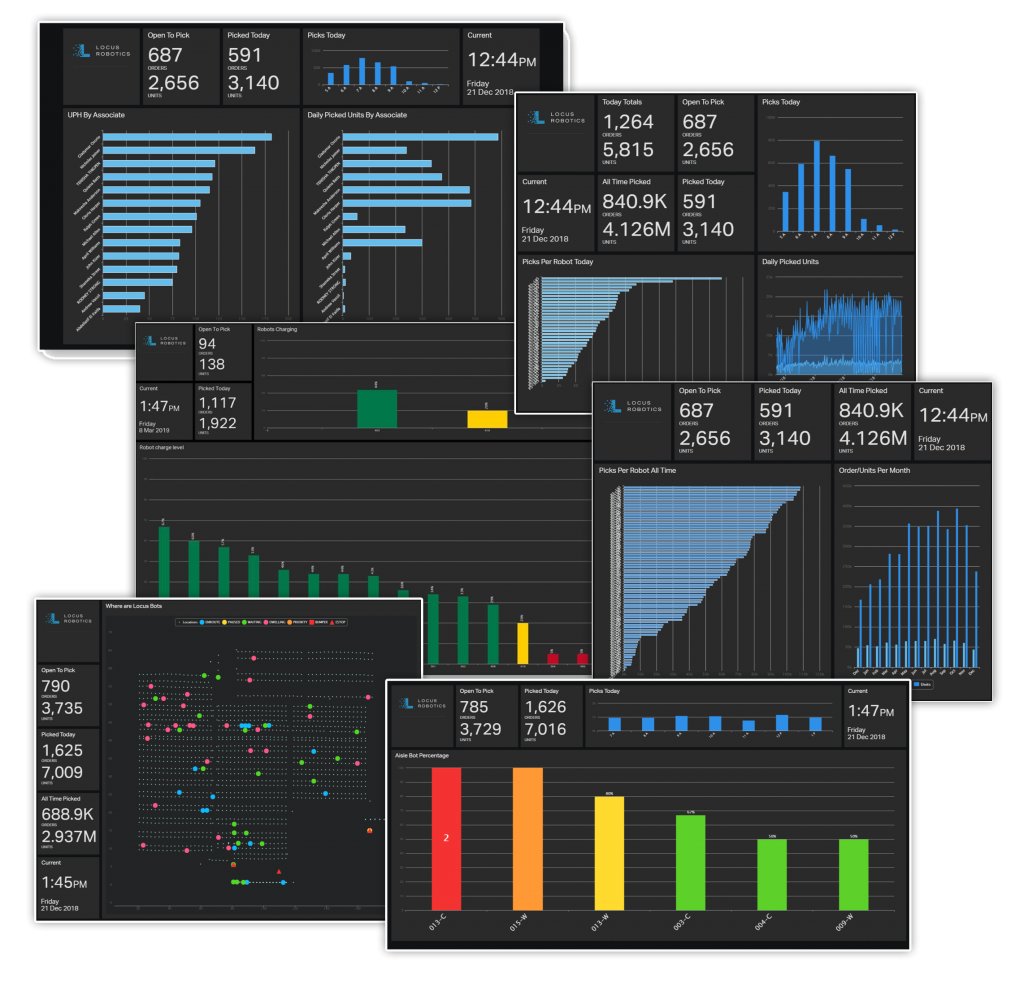
Business Intelligence for Making Informed Decisions
Current state-of-the-art automation comes with a data-rich reporting of all of your key metrics such as hourly, daily, and monthly performance metrics, individual worker performance, inventory flow, slotting optimization, workflows, work heat maps, current and historical rates, charging and status information and more. This wealth of information which can be accessed real time provides invaluable insights for making informed decisions about managing processes as well as planning, forecasting and makes it easy to align your business goals with personalized worker goals.
Affordability: Start Small, See Rapid ROI, Scale up
Financial considerations play a crucial role in any decision-making process. With entry-level automation solutions, you can start small, see the undeniable ROI in as little as a couple of months, and then scale up according to your needs and available financing. You have the freedom and flexibility to make incremental tweaks, stay nimble and responsive to changes in demand, while aligning automation investments with your business growth.
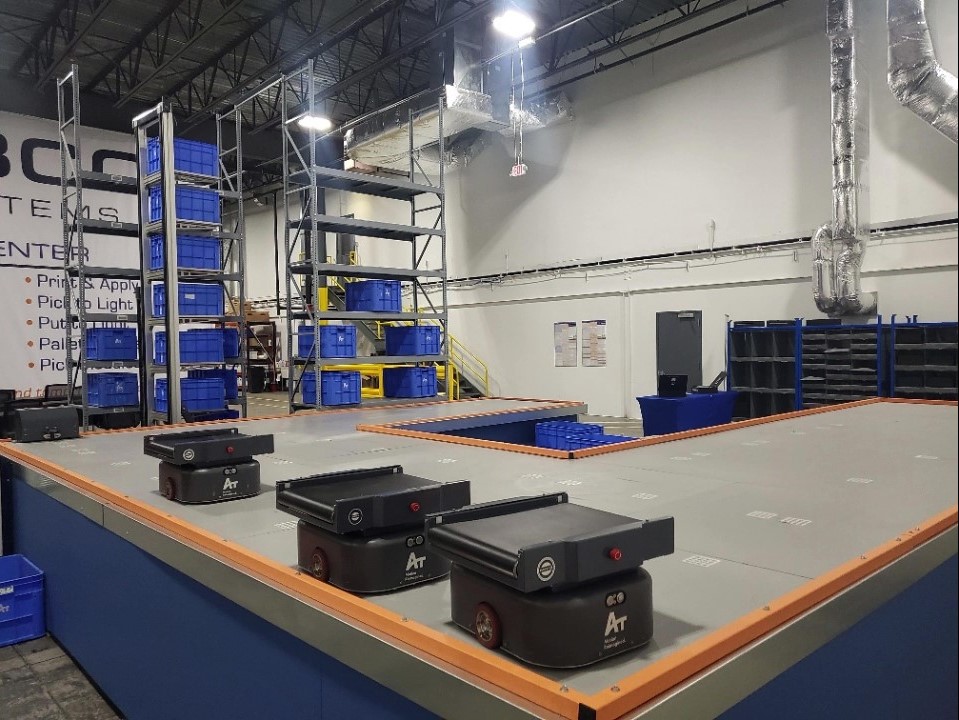
Visit ABCO’s Showroom, Where Revolution Begins
Curious to see the future of warehousing operations firsthand? In our showroom at 372 Starke Rd, Carlstadt, NJ, you can see the latest automation technologies up close, discover how they improve material handling and gain valuable insights into their practical applications. Our experts will be on hand to guide you through the possibilities and help you identify the perfect fit for your business. Whether you’re interested in warehouse automation, conveyors & sorters, warehouse robotics, or any of our other services, we invite you to come and see the potential for yourself. Reach out to us today and schedule a visit!
Oct 10, 2023 | ABCO Systems, AGV, AMR, Automation, E-commerce, order fulfillment, Robotics, Supply Chain
In the labyrinth world of modern warehousing, where precision and efficiency reign supreme, the emergence of Autonomous Guided Vehicles (AGVs) has been nothing short of revolutionary. AGVs are able to navigate through this intricate maze, transforming the way businesses handle material transport within their facilities. In this guide, we embark on a journey through the winding paths of AGVs, unveiling their capabilities, diverse applications, and the manifold benefits they bring to the logistics and warehousing business operations.
AGVs: The Vanguard of Automation
Autonomous Guided Vehicles (AGVs) are self-contained, self-propelled robotic vehicles engineered to perform material transport tasks autonomously. These tireless machines navigate through warehouses using an array of navigation systems, each with its unique advantages and applications.
The Navigation Spectrum
AGVs use several different types of navigation systems, each designed to suit specific environments and tasks:
Magnetic Guide Tape: AGVs equipped with magnetic sensors follow predefined paths marked by magnetic tape on the floor, making them ideal for precise, repeatable routes.
Wired Navigation: Wired navigation uses embedded wires or cables in the floor to guide AGVs, ensuring they remain on their designated paths.
Laser Target Navigation: AGVs use lasers to identify and follow reflective targets placed strategically throughout the warehouse, providing flexibility in route planning.
Inertial Navigation: These AGVs rely on accelerometers and gyroscopes to track their movement, making them adaptable to dynamic environments.
Vision Guidance: Vision-based systems use cameras and machine vision algorithms to navigate, offering high flexibility and adaptability.
Geoguidance: These systems utilize natural features like landmarks or magnetic fields for navigation, ideal for outdoor or non-standard environments.
LiDAR: AGVs equipped with LiDAR sensors create detailed maps of their surroundings, enabling precise positioning and obstacle avoidance.
Applications for AGVs
AGVs are versatile workhorses with applications spanning various industries:
Automated Guided Carts: Ideal for carrying smaller loads and materials within factories and warehouses.
Forklift AGVs: Equipped with forklift mechanisms, these AGVs excel in pallet handling and are commonly used in logistics and distribution centers.
Towing AGVs: These AGVs tow multiple carts, optimizing material flow and reducing the need for manual transport.
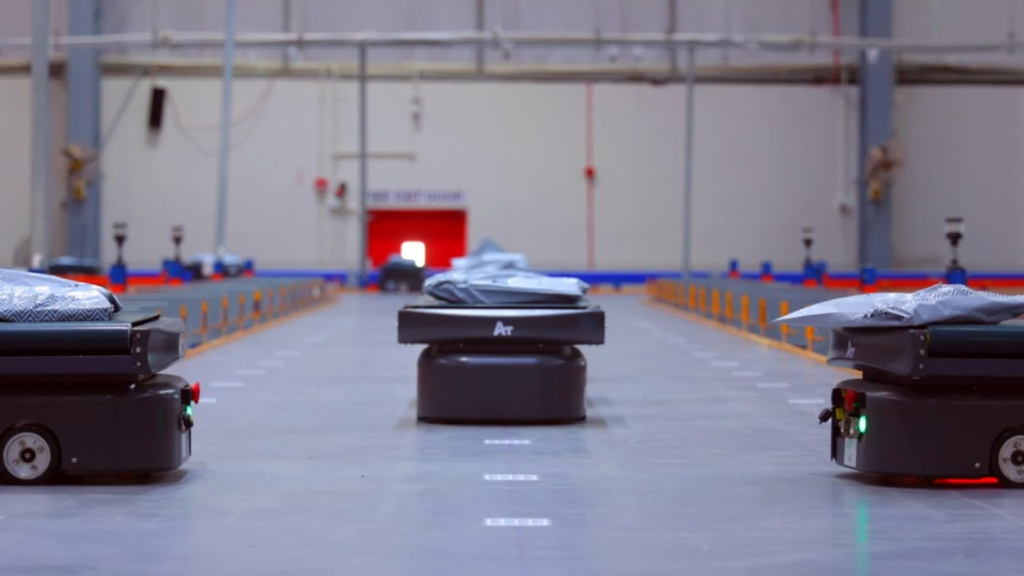
Unit Load Handlers: Designed for heavy lifting, unit load handlers excel in moving large, single items.
Heavy Burden Carriers: These robust AGVs are built for transporting exceptionally heavy loads, making them indispensable in industries like automotive manufacturing.
Autonomous Mobile Robots (AMRs): AMRs are highly adaptable AGVs that can be programmed for various tasks, from material transport to collaborative operations with human workers.
Benefits of AGVs
The adoption of AGVs in warehouses and manufacturing facilities yields a multitude of benefits:
Increased Efficiency: AGVs operate 24/7, reducing downtime and increasing productivity. Their precise navigation minimizes travel time and optimizes material flow.
Enhanced Accuracy: AGVs are programmed to follow predefined routes with exceptional precision, reducing the risk of human error in material handling.
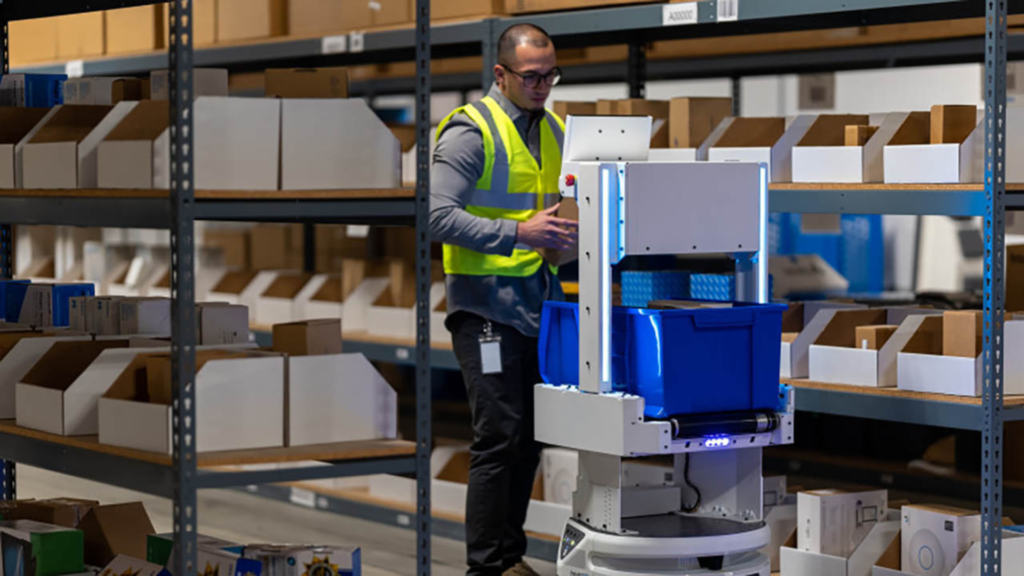
Labor Cost Reduction: With AGVs handling routine tasks, human workers can focus on higher-value activities, leading to labor cost savings.
Space Optimization: AGVs can navigate in tight spaces and vertical storage environments, making the most of available storage space.
Safety: AGVs are equipped with safety features such as obstacle detection and collision avoidance systems, ensuring a safe working environment for both robots and human workers.
Flexibility and Scalability: Warehouses are dynamic environments, and AGVs are designed to adapt. They can be reprogrammed or reconfigured swiftly to accommodate changes in product types, demand patterns, or operational layouts. As businesses grow, AGV fleets can also be easily expanded or reconfigured to adapt to changing needs.
Conclusion
By better understanding the classifications, navigation systems, applications, and potential of AGVs, businesses can make an informed decision on which AGV is right to streamline their operations, enhance accuracy and improve safety. Reach out to us today to get world class consulting and explore the potential of AGVs and the great opportunities they bring to the world of warehousing.
Oct 3, 2023 | ABCO Systems, Automation, Conveyor, Maintenance, Robotics, Sortation, White Paper
In today’s fast-paced world of material handling and logistics, automation is the name of the game.
But how do you ensure your automation equipment not only performs at its best, but also stands the test of time? Dive into our latest White Paper where we provide a detailed guide how to achieve equipment longevity. Also, discover how ABCO Systems can be your trusted partner in this journey, with our unmatched expertise in automation equipment maintenance and servicing.
Don’t miss out on this essential read!
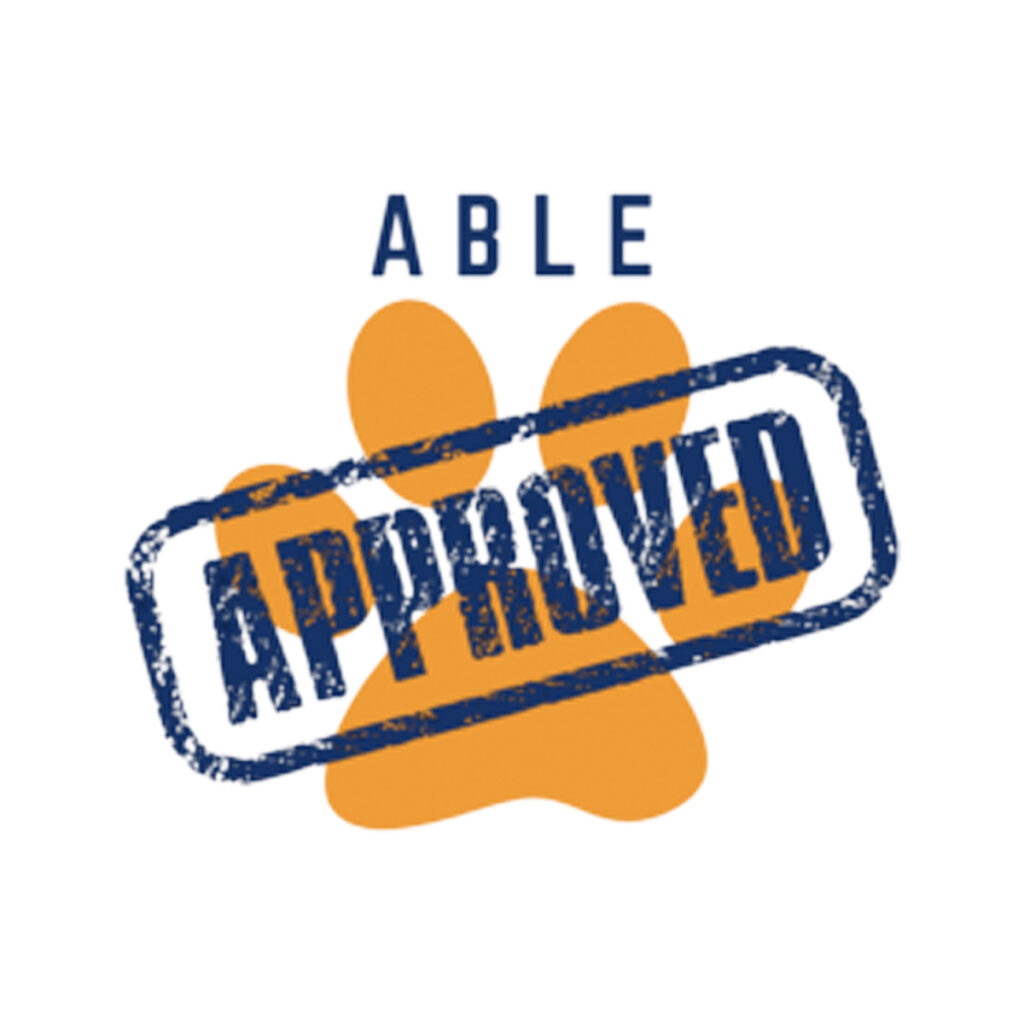
Click the “Able Approved” icon to download the “Ensuring Longevity: Maintenance and Servicing of Automation Equipment” – White Paper.